Contatto Editoriale:
Paolo Lista,
Lista Studio srl®
Borgo Belvigo 33, 36016 Thiene Vi ITALY
tel/fax 0445,372479 o info@lista.it
Biomedical engineers use simulation software to
study the human body at the University of Tenessee, Memphis, Usa
While mechanical engineering software is commonly used for designing,
analyzing and testing car and airplane parts or other complex mechanical
systems, its ability to simulate dynamic conditions also lends itself
to studying the movement and mechanics of the human body.
At the School of Biomedical Engineering
(BME) at the University of Tennessee,
Memphis, graduate students in a biomechanics course develop mechanically
equivalent models of bone-joint systems using Working Model(r) software
and apply engineering principles to study the body's musculoskeletal
systems.
Biomechanical engineers conduct research to characterize the motion
of human joints for different health conditions, including normal,
pathological, injured, or surgically altered. An understanding
of a joint's movement can be used to diagnose its health or monitor
the progress of different rehabilitative techniques used to restore
joint mobility and function. Their research may even lead
to improvements in surgical techniques or design of joint implants.
"Engineering theory of mechanisms and linkage systems can serve
as a basis for studying human joint movement and mechanics," says
Denis DiAngelo, Ph.D., a mechanical engineer and assistant professor
in the School of Biomedical Engineering. "While it is common
to use graphical methods or analytical techniques to analyze linkage
systems, Working Model enables students to study the continuous range
of motion of bone-joint systems, whether the knee, finger, hip, or
spine."
Working Model uses many engineering principles familiar to the BME
students, such as kinematics, dynamics and numerical methods, and serves
as a tool for students to apply this knowledge to study
medical-related problems. The muscle-joint systems are modeled as
a network of rigid bodies with curvilinear contacting surfaces or pinned
joints connected by various mechanical components,
including springs, dampers, and pulleys, which simulate the muscles or
ligaments. Properties of the mechanical components can be defined with
mathematical expressions to simulate the non-linear structural properties
of tissue elements, while motors, actuators, sliders, or cable systems
regulate the motion or load applied to the joint system.
The graduate BME program is located on the university's medical campus,
and is one of only a few programs in the U.S. offering graduate BME degrees,
a broad area of education combining mathematics, engineering and physics
to study medical-related problems. Some graduate students in the BME
program specialize in imaging, cell and tissue engineering, or blood flow
mechanics. Others study joint implant mechanics or design prosthetic limbs.
Motion Study Solutions
According to DiAngelo, biomechanists often analyze human movement
with camera-based motion analysis hardware equipped with custom software
programs. The bone segments and joints are represented as
rigid links connected by simple pinned joints that are displayed as
stick figure images.
Unfortunately, modeling the human joint as a simple pinned connection
does not characterize its true, natural motion.
For students, being able to visualize realistic movement of a joint
is critical to understanding the interaction between the joint anatomy
and the surrounding muscles and ligaments.
Other simulation techniques
use mathematical expressions to define the contact surfaces and muscle
and ligament mechanics. Many of these programs require extensive
development, and do not provide animation features standard in Working Model.
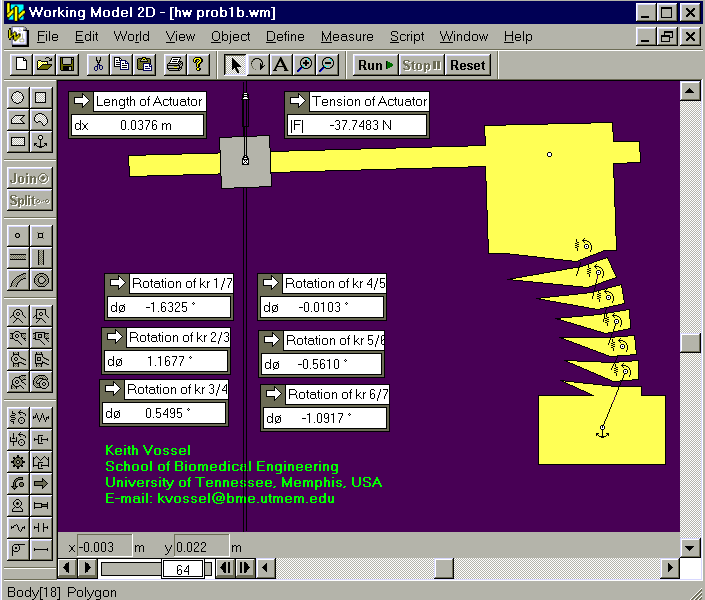
In this picture there is a copy of a Working Model simulation of the cervical
spine loaded in extension. This model demonstrated that when the moment
arm is attached to the actuator with a pin joint rather that a pin joint
with a linear bearing, the motion in the sagittal plane is constrained
and the moment response of the cervical spine becomes excessive after
only a few degrees of global rotation. Note that the cervical spine is
inverted so that T1 is in the upper pot and C2 is in the lower pot.
Courtesy of Keith Vossel, BME, E-mail kvossel@bme.utmem.edu
While several solid modeling programs, such as Pro/ENGINEER or Adams,
could be used to study joint movement, many academic budgets cannot
support expensive, workstation-based software.
In 1994, DiAngelo considered the alternatives and installed
Working Model software from Working Model, Inc. Today, biomedical
engineering students work on a network of Pentium-based PCs running
Working Model 2D and 3D software.
"We're really excited about the discoveries we're making
with Working Model," DiAngelo says. "At the same time,
we'd like to inform biomedical engineers of the many practical ways
Working Model can advance their work once they see how we've incorporated
the software into our teaching and research activities."
While DiAngelo praises Working Model, he also stresses the importance
of understanding how the program manipulates the user-defined parameters
to achieve a solution. The message DiAngelo gives his students is
"check yourself."
"I ask students to solve problems with known solutions.
This step enables them to understand how the software works,"
DiAngelo continues.
Modeling Joint Movement
DiAngelo's class has studied spine mechanics using Working Model.
The class looked at the upper neck region-the cervical spine-which
encounters a great deal of movement during normal daily activities.
According to DiAngelo, the complexity of the cervical spine continues
to challenge biomechanical engineers.
First, DiAngelo and his students imported digitized X-rays of a spine
into AutoCAD(r) design software from Autodesk, Inc. Next, anthropomorphic
and morphometric data from the adult population were used to generate a
parametric model of the spine. Using AutoMotion(tm), students exported
the CAD files directly into Working Model for simulation.
To study the mechanics of the spine, load and motion data from experimental
studies performed in the research lab were imported into the model.
To properly model the experimental set-up, additional mechanical components
were added to the spine model that represented the testing apparatus
and mounting fixtures.
Thomas Jansen, a BME graduate student, recently won multiple
student competition awards at a biomedical engineering conference
based on research using the cervical spine model. The simulation study
looked at the influence of joint placement on spine kinematics. According
to DiAngelo, it is often difficult to replicate the natural physiologic
motion of human joints using mechanical testing machines. But, using the
simulation model, Jansen studied different configurations to determine
an optimal testing arrangement that more closely simulated the natural
motion of the spine. Simulation studies like this help standardize
biomechanical testing protocols for joint implants.
Real World Applications
DiAngelo envisions many real-world Working Model applications
for biomedical engineers to work with surgeons, physical therapists,
and others who work in biomechanics and rehabilitative medicine. For
instance, simulation teaches therapists and biomedical engineers how
the different ligaments affect the motion and stability of the joint.
According to DiAngelo, Working Model would enable physical
therapists treating knee injury patients to recognize the diagnosis
and set appropriate treatment plans. Similarly, a better understanding
of the knee's anterior cruciate ligament may enable biomedical engineers
to improve ligament replacement designs.
Future Directions
After graduation, many of the BME students find employment with
implant or device manufacturing companies, while others go on to work
at university centers or health-related government agencies.
What all of these students share is a unique approach to understanding
the human body's movement and mechanics.
Eventually, biomedical engineers believe that by understanding
the way joints move, they'll be able to design artificial joints and
medical devices that function well with the human body. They'll
also understand how the ligaments and muscles contribute
to the movement and mechanics of the joints. While researchers
continue to solve medical problems, biomedical engineers at the
University of Tennessee, Memphis believe their work with Working Model
will help validate and refine those solutions. In the end, this will
save valuable research time and have a significant impact on
patient welfare and health care costs.