Contatto Editoriale:
Paolo Lista,
Lista Studio srl®
Borgo Belvigo 33, 36016 Thiene Vi ITALY
tel/fax 0445,372479 o info@lista.it
IL GRATTACIELO PIÙ ALTO SENZA VIBRAZIONI
World's largest tuned mass damping system engineered with MSC.visualNastran 4D, opens a potential multi-million dollar market to design/build, consulting engineer firm.
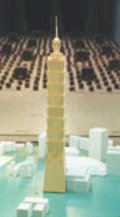
At a planned height of 508m, the Taipei Financial Center, in Taiwan, will be the world's tallest building, at least for this year. Because of its height and location in a typhoon region, the Taipei Financial Center is subject to wind-induced sway motion, resulting in higher than desirable accelerations that could cause occupants of the upper levels to feel discomfort. Engaged to reduce these accelerations with a vibration damping system, are Motioneering Inc. and sister company RWDI Inc. of Ontario, Canada, design/build, and consulting engineering firms specializing in, among other things, wind-induced vibration. Mr. Brian Breukelman, principal, says, "We are providing an 800 ton tuned mass damper (TMD) that swings when wind acts on the building, absorbing energy and reducing the building's accelerations by 30 to 40%. It will be the largest TMD ever built. We utilized MSC.visualNastran Motion software in the design process of the TMD system subcomponents, and are using the time domain solver to investigate the impact of seismic events on the design of the travel limiting snubber system. We're also testing 3D solid models of the individual components, so when the building starts to move, we can ensure that interferences between components are prevented."
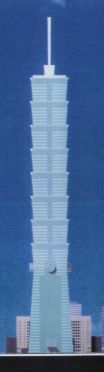
In order to build taller skyscrapers like this, structural engineers are resorting to lighter weight materials, which usually result in more flexible structures that are therefore subject to more vibration. Mr. Breukelman says, "We come into play when the primary cause of vibration is wind. As a result, even though we design a system for wind, we are forced to look at other things that can cause vibration, including seismic activity."
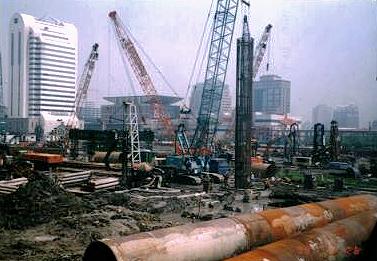
A TMD is a passive damping system that is comprised of a secondary mass attached to a vibrating structure. Essentially, a TMD can be considered an energy sink, where excess kinetic energy built up in a building or bridge by the wind, is transferred to the secondary mass. Mr. Breukelman explains, "The TMD, in the Taipei system, is a natural pendulum. The length of the cables give it a natural frequency, very similar to the building's frequency, and when the building starts to vibrate, the damper will start to move due to the similar frequencies. But due to the physical properties of the system, the damper moves out of phase with the building. If the building moves east, the damper moves west. The damper doesn't stop the building from moving, but it does reduce the motion to acceptable levels. We also needed to look at what would happen as the damper moves when the building responds to an earthquake. With MSC.visualNastran, we can input actual recorded seismic time histories and graphically see what's going to happen to the TMD and the building, as well as output engineering data."
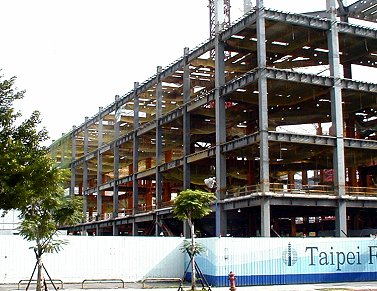
To better predict the behavior of TMDs, engineers utilize MSC.visualNastran Motion software to analyze kinematic characteristics of 3D solid models in simulated motion analyses. This enables designs to be optimized by investigating a large number of load conditions and physical geometries, leading to improved designs and fewer changes during fabrication of the TMD components and resulting in more cost-effective designs. Mr. Martin Bliemel, Technical Coordinator, explains, "We use MSC.visualNastran Motion in several areas, including testing the entire TMD system through its full range of motion, including collision detection. On less recent projects designed in 2D, collision detection was very difficult to do, whereas in 3D it's very easy. The other area is determining if the TMD will actually exceed the designed range of motion during a seismic event, which requires analysis of the TMD subassemblies, or individual components. Seismic events are modeled using time histories of actual earthquakes, and wind events are modeled using post-processed wind tunnel data and meteorological data."
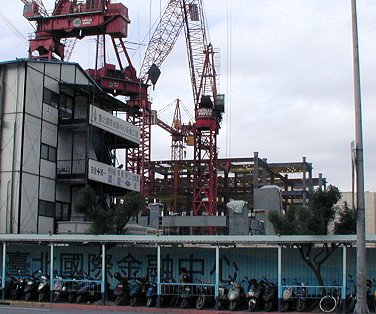
An unusual feature of the Taipei Financial Center is that the damping system is exposed on two floors, a restaurant bar lounge and an observation level. The center of the spherical-shaped mass is one meter above the floor in the restaurant and bar and the observation level provides an overhead view from an elevation above the TMD. Mr. Breukelman says, "The Taipei project blends a lot of disciplines, including architecture, engineering and interior design. Most damping systems are relegated to some mechanical space where nobody ever sees them. You'll be able to sit and watch the Taipei TMD while sipping your favorite cocktail."
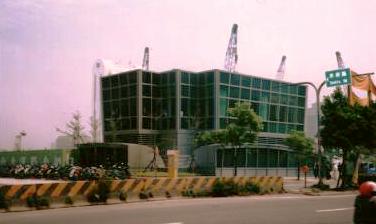
Engineers can import 3D CAD solid models into, or create basic solid models within MSC.visualNastran Motion and 4D, the latter of which integrates FEA technology in order to test the range of motion of a component or of subassemblies. Mr. Bliemel says, "Where we're concerned with the geometric extremity and solids colliding with each other, we'll import 3D CAD solid models. However, if we're determining the range of motion in response to a seismic event, where we're more concerned about the inertial properties of the mass and the shape is less important, we utilize the default CAD entities supplied within MSC.visualNastran Motion."
Simulation of 3D solid models enables engineers to better understand the behavior of a structure's dynamic properties and loads. In the past, an engineer would have to make assumptions for things that couldn't be modeled. By using MSC.visualNastran Motion, engineers have a tool to model very complex engineering problems. Mr. Breukelman says, "Potentially, it saves material costs because if it can't be modeled, the forces would be estimated very conservatively. By modeling the problem, the engineer can optimize the design, while still ensuring that the design meets all code requirements and has appropriate safety factors. The other benefit is the ability to manipulate any sort of mathematical function without choosing the default functions, for example, in order to accurately model the non-linearities of damper forces, or even displacement of an object over time."
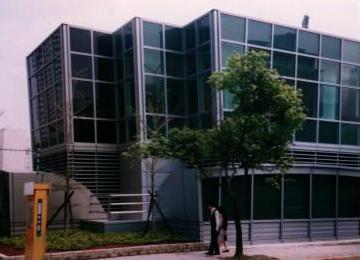
Mr. Breukelman adds, "We were able to input forces of our own determination, which is necessary as you get into more complex engineering problems. For instance, MSC.visualNastran Motion enables an engineer to define any state variable (e.g. position, velocity, acceleration, orientation) or force as a function of virtually any combination of any other system state variables or user inputs, with any exponent on the proportionality. For example, a simple shock absorber has what is called a V-squared relationship, in which force is proportional to velocity squared. If this is the only thing that we could do, then there would be a lot of situations that we couldn't model. But with MSC.visualNastran 4D we can input a non-linear damper where the force is proportional to velocity to the exponent of any real number. A damper can be modeled with a velocity exponent of less than one, which is what is often used in seismic applications. The nonlinear capability and the ability to input our own forces make the software very useful. The ability to input existing data acquired through wind tunnel testing as performed by sister company RWDI, and from seismic time histories which have been either synthesized from code spectra, or measured near the site, provides an additional bonus. Rather than specifying equations of force, we can just say the force is a relationship as a function of several thousand lines of file data on displacement versus time."
OTHER 83 DIFFERENT APPLICATIONS !
ALTRI 83 CASI IN SETTORI DIVERSI !