Contatto Editoriale:
Paolo Lista,
Lista Studio srl®
Borgo Belvigo 33, 36016 Thiene Vi ITALY
tel/fax 0445,372479 o info@lista.it
ROKENBOK'S DOWN-A-VATOR MADE WITH WORKING MODEL
Simple toy, complex mechanism
Toy makers use mechanism analysis to simulate the action of toys with moving parts. Sometimes they do this to address safety concerns and sometimes they do it to make sure they've got the motion they want. Sometimes both issue are important, as they were on the Rokenbok Down-A-Vator
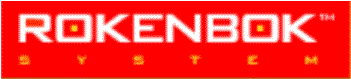
If You haven't bought toys for a while, you may not be familiar with the Rokenbok system. It was introduced in 1997 and has won numerous awards since then. Basically, it is a construction environment, fully compatible with Lego, that children use to create buildings, highways, bridges, and chutes. The idea is to create a multilevel environment in which to drive radio-controlled Rokenbok trucks.
The Down-A-Vator is a Rokenbok accessory that uses pneumatic power (no batteries required) to lower a vehicle like a one-way elevator. After the child drives a vehicle onto its platform, the Down-A-Vator returns to the up position.
The Down-A-Vator's mechanism, a four-bar linkage, was a critical design element because the platform had to remain horizontal while traveling though a very specific range of motion that allowed it to lower the vehicle and raise itself up again to exactly the right height. Moreover, Rokenbok didn't want any scissoring action that could hurt a child's finger.
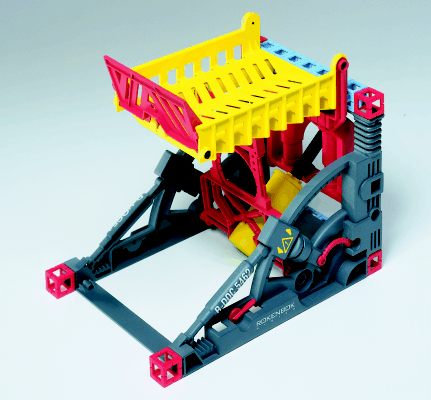
It certainly would have been possible to design that four-bar linkage by hand. Engineers would have made a mockup of the mechanism with cardboard and push pins and fiddled with it until they got the motion they needed. Then they would have performed basic engineering calculations to determine mechanical characteristics, such as how much spring force was needed and where it should be applied to raise the empty platform back to its starting position. Additional calculations would have told them how much damping was needed so that the vehicle didn't drop too quickly to the lower level. "Engineers have made four bar linkages without computers", says Dan Aldred, manager of product development at Rokenbok Toy C. (Encinitas, CA, USA). "But now it's easier and faster". Aldred used Working Model from MSC Working Knowledge to perform the mechanism analysis on the Down-A-Vator. At that time, Working Model was only a 2D program, so he actually started the entire design for the product in Working Model. He began by sketching out a 2D line drawing of the linkage, specifying which lines were rigid and which could bend, which line was a spring and which was a damper, and were the pivot points were located. He then specified the size of the spring and the damper and applied a 500 gram load to the mechanism to represent the weight of the truck.
When he clicked "Play", the software ran the mechanism through its range of motion. Besides providing a clear image of the motion path, the software calculated the spring and damping forces and presented them in an easy-to-understand graph. Aldred could immediately see if the mechanism was performing as desired. "The beauty of doing it this way", Aldred says, "was that I could change the size of my spring or damper or the amount of the applied load and run the analysis again. It only took a few seconds for the computer to change the parameters and perform the calculations."
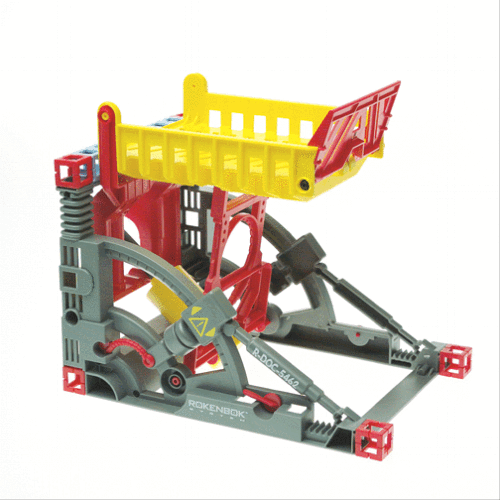
Aldred repeated the mechanism analysis until he had the Down-A-Vator's mechanism working exactly the way he wanted. He then used the final 2D sketch as the basis for modeling the rest of the product. Today, since Working Model supports 3D and now even "4D" (which means FEA analysis together with 3D motion analysis), Aldred says he would begin the design by creating a solid model in SolidWorks. He would include the pivot points, locations of the spring, and related information in the solid model, then use the solid geometry directly for the Working Model mechanism analysis.
This example involves a single mechanism on a single toy, but it saved Rokenbok one or two weeks of work, according to Aldred. Multiply that by all the toys with moving parts that are introduced each year and you can see what this software tool alone could mean to toy makers. In this industry, the full spectrum of design-automation technology is becoming a requirement. Taking advantage of technology has become the key to developing products that children will treasure, and delivering them at an ever-faster pace.
Adapted by Caren Potter
Computer Graphics World
Reprinted with permission from:
Computer Graphics World, November, 1999
www.cgw.com
OTHER 83 DIFFERENT APPLICATIONS !
ALTRI 83 CASI IN SETTORI DIVERSI !